- Swiss testing laboratory
PPE Apparel Test

Hassle-free testing experience
Need to get a product tested? No worries! To and fro logistics are on us; we collect your products, test them and, deliver them back to you.
Related tests for you
Abstract
PPE apparels play a vital role in the protection of individuals from exposure to various occupational and environmental hazards including biological, chemical, physical, and thermal hazards. Therefore, the efficacy of PPE apparel is important to ensure the safety of people during high-risk operations in medical facilities, construction locations, and other industries. PPE apparel testing ensures that all such equipment performs as expected in terms of providing protection against various hazards while making sure that these equipments comply with regulatory standards.
The scope of PPE apparel testing is very wide and comprehensive, as it covers various protective gear ranging from clothing to face shields, goggles, and more. Testing ensures that the equipment is resistant to environmental stressors, prevents exposure to harmful substances, and performs its function over an extended time. The testing normally involves systematic tests, where the PPE is subjected to hazardous conditions mimicking real-life situations and determining whether the product can provide sufficient protection without impacting comfort and usability.
Do you have a product that needs testing?
PPE apparel test conditions
For proper assessment of PPE clothing, testing is done in conditions that mimic real life. To achieve this, various conditions are closely monitored depending on the type of equipment being tested and the specific hazards it provides protection against. Some common test conditions include:
- Temperature variations
The PPE should be exposed to high and low temperatures to check its performance at extreme temperatures. Some materials break down at high temperatures, while cold temperatures may affect flexibility and fit, which are of paramount importance for maintaining protection.
- Humidity levels
PPE clothing apparel, especially protective suits and gloves, are often subjected to humid testing to monitor whether they retain moisture, remain breathable, and the comfort level felt by the wearer.
- Exposure to chemicals and contaminants
Some PPEs are made with material that protects the wearer against dangerous chemicals or biological contaminants. Testing ensures the material can resist chemical penetration to prevent the transmission of harmful pathogens.
- Mechanical forces
PPE is also tested for mechanical stresses such as abrasion, puncturing, and tearing to check whether it can sustain physical wear and tear. This is important for PPE equipment used for extended use in demanding environments.
These diverse testing circumstances offer a thorough assessment of the performance of PPE in various work settings, guaranteeing both the safety and effectiveness of the gear.
Test organisms
Target microorganisms for PPE apparel testing depend on the intended purpose of the equipment. At MIS, generally, personal protective equipment tests are performed against Staphylococcus aureus and Escherichia coli, as these organisms are common infectious agents found in high-risk environments such as healthcare facilities and public spaces. Additional strains can be tested at the customer’s request.
PPE apparel test parameters
PPE apparel testing has specific parameters. These include:
- Material integrity
The materials used for PPE must not lose their protective properties after repeated usage. Testing assesses aspects such as tear strength, resistance to punctures, and seam integrity.
- Breathability
Products like masks and protective clothing have to provide enough breathability with sufficient air exchange without compromising protection.
- Resistance to liquids and particulates
PPE equipment, for example, gowns and gloves, should be resistant to penetration by liquids and prevent the infiltration of harmful particulates.
- Comfort and fit
Testing must ensure that the gear fits properly and remains comfortable during extended periods of use, without compromising its protective functions.
Test product information
PPE apparel testing encompasses a comprehensive range of protective products, including but not limited to:
- Protective clothing: These include full-body suits, coveralls, and gowns designed to protect the wearer from hazardous substances such as chemicals and biological agents.
- Respiratory protection: Masks and respirators which filter harmful airborne particles, gases, and pathogens.
- Eye and face protection: Goggles, face shields, and visors which protect against splash impact and airborne contaminants.
- Hand and foot protection: Gloves and boots that have chemical resistance, electrostatic conductive, or dielectric properties and also personal protective equipment to prevent injuries from mechanical impacts.
Each product type is tested with regard to the specific intended protective function to ensure thorough evaluation and certification.
PPE apparel test methodology
The testing methodology of personal protective equipment is different for each type of protective equipment. This is because different PPE products serve different purposes such as respiratory protection, or shielding against physical hazards. These properties demand different testing methodologies to be effectively assessed. Below is an overview of various testing methodologies applied across various categories of PPE:
- Physical and mechanical testing
This testing involves assessing the physical properties of PPE. This includes the tensile strength, tear strength, puncture resistance, and flexibility of gloves, protective suits, and footwear. It provides a guarantee that these materials withstand mechanical stress and don’t lose their protective qualities.
- Chemical permeation testing
For PPE, chemical resistance testing is essential, especially when it is used in environments where the wearer is exposed to harmful chemicals. This test method determines the time taken by the chemicals to permeate into the material and checks how efficient the material is in safeguarding the wearer against exposure to various substances.
- Thermal and flame testing
PPE designed for thermal resistance, such as a firefighting suit, flameproof garment, fire-resistant coveralls, etc are evaluated for resistance to the passage of heat and direct flame.
- Biological Protection Testing
Besides the above-mentioned tests, PPE apparel testing for protection against biological hazards like bacteria and viruses is also important. At MIS, we perform PPE appeal testing using standard test protocols such as ASTM F2100, ASTM F2101, and EN 14683. These test methods are specific for the type of product being tested.
ASTM F2101: ASTM F2101 is a standard method to assess the bacterial filtration efficiency of medical masks. It determines the effectiveness of medical face masks in filtering aerosolized bacteria by comparing upstream and downstream residual concentrations of bacteria.
ASTM F2100: ASTM F2100 specifies several test standards for assessing various aspects of medical face masks. These include:
- ASTM F2299 which is specifically designed to test the capability of the medical face mask for filtering viral-sized particles.
- ASTM F1862 is used to determine the mask’s resistance to the penetration of synthetic blood at different pressures.
- MIL-M- 36954C is a test to quantify the breathability of the mask in terms of differential pressure expressed as mmH2O/ cm²
EN 14683: EN standard to assess the quality and performance of medical face masks
ISO 22609: A test method for measuring the resistance of medical face masks to penetration by a splash of synthetic blood.
These tests are critical in healthcare settings, where the use of personal protection equipment is a must to prevent the spread of infectious agents.
Importance of PPE apparel test
The significance of the personal protective equipment test lies in its ability to validate the safety and functionality of equipment meant for protection in hazardous environments. Properly tested PPE equipment minimizes the risk of injuries, infections, or exposure to poisonous chemicals. Conducting thorough tests enables manufacturers to ensure that the products work as expected in real conditions.
PPE apparel testing also helps manufacturers meet regulatory requirements and ensure that they provide effective equipment to their employees. It contributes to the protection of individuals, reduces the liability for businesses and enhances workplace safety.
Compliance and industry standards for PPE apparel test
PPE apparel testing must adhere to specific compliance standards and industry regulations to guarantee the safety and dependability of the products. Various international standards offer guidance for assessing different features of PPE apparel. Some of the important standards include:
- ISO 16604 – Assesses the resistance of protective clothing materials to penetration by blood-borne pathogens.
- EN 14126 – A testing method for reusable and limited-use protective clothing that safeguards against infectious agents.
- ASTM F739 – A standard test procedure for the permeation of liquids and gases through protective clothing materials under continuous contact conditions.
- ISO 13997 – Measures the resistance of protective clothing to cutting by sharp objects.
- ASTM D3577 – A standard for testing different attributes of rubber surgical gloves.
- ASTM D6319 – An international standard for assessing the performance and safety of nitrile rubber gloves used in medical settings.
- ISO/TS 20141 – Offers guidelines for the compatibility testing of PPE.
Adhering to these and other relevant standards ensures that PPE apparel is effectively tested and deemed safe for use in the appropriate environments. Manufacturers are required to comply with these standards to gain regulatory approval and certification for their products.
Advantages of PPE apparel test
- Ensures maximum protection
Extensive testing ensures that the PPE apparel is tough enough to hold against various hazardous conditions and protect the wearer from potential risks.
- Increases product durability
Materials are tested for resistance to both physical and environmental stress; testing helps enhance the overall durability and reliability of a product.
- Regulatory compliance
The test ensures that PPE products adhere to the required regulation, which supports market entry and is certified.
- Promotes user safety
Well-tested PPE provides users with confidence, knowing they are protected against hazards in their work environments.
Conclusion
PPE apparel testing is the most critical process that protects the wearer against various hazards and ensures efficacy while exercising regulatory compliance. Proper testing under different conditions and environments guarantees that apparel produced by companies meets the highest standards of safety and performance. As a result, organizations can provide their workers with reliable protection, ensuring their safety and well-being in hazardous environments.
For reliable PPE apparel testing services that adhere to the latest standards, contact our experts at Microbe Investigations Switzerland. We offer comprehensive testing solutions tailored to ensure your PPE products meet industry requirements and provide maximum protection.
Frequently Asked Questions
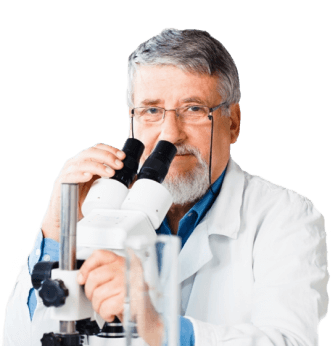
DR. Martinoz Scholtz
PPE apparel including protective clothing, face guards, eye goggles, gloves, respirators, and other personal protective equipment are tested.
Standards such as ISO 16604, EN 14126, and ASTM F739 are commonly used for testing the effectiveness of PPE against biological and chemical hazards.
Durability is evaluated through mechanical tests such as tear resistance, abrasion resistance, and puncture tests to ensure long service operations.
Chemical resistance tests establish the effectiveness of PPE materials in resisting chemical permeation.
PPE is exposed to bacteria, viruses, and other pathogens to observe whether the material prevents microbial penetration.
Fit and comfort are determined through ergonomic testing and wear trials to ascertain that usability is not compromised while ensuring proper protection.
Yes, high-visibility PPE is tested for visibility under different lighting conditions using the standard ANSI/SEA 107.
PPE is subjected to tests for high voltage, resistivity, leakage current, and dielectric strength in accordance with standards such as ASTM D120.
Evaluations of thermal manikin performance, radiant heat exposure, heat transfer, evaporative resistance, and flash fire tests are conducted to determine protection in heat environments.
Meet the best of the blend of
R&D, Efficacy Testing,
Innovation and Passionate
Experts at MIS.
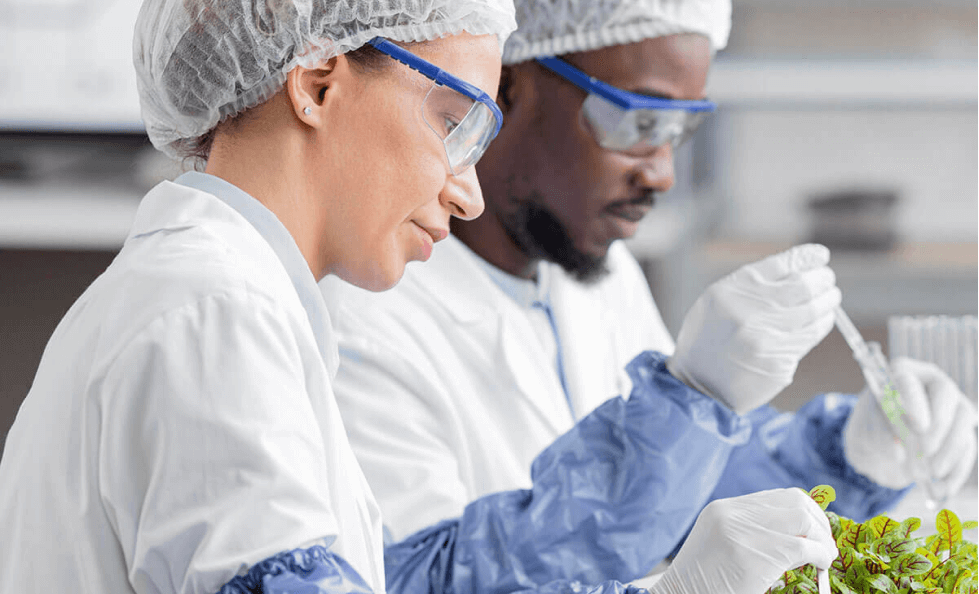
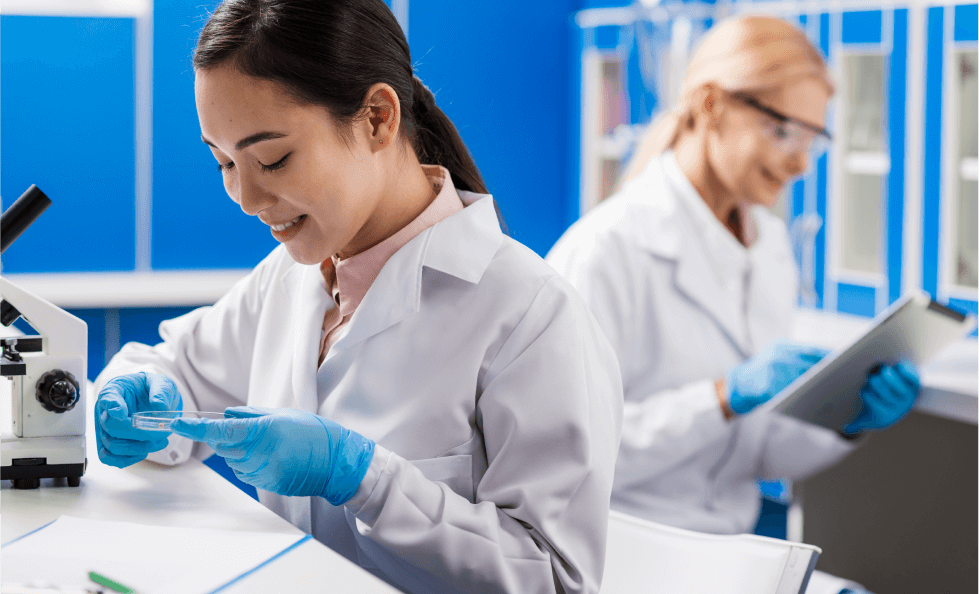
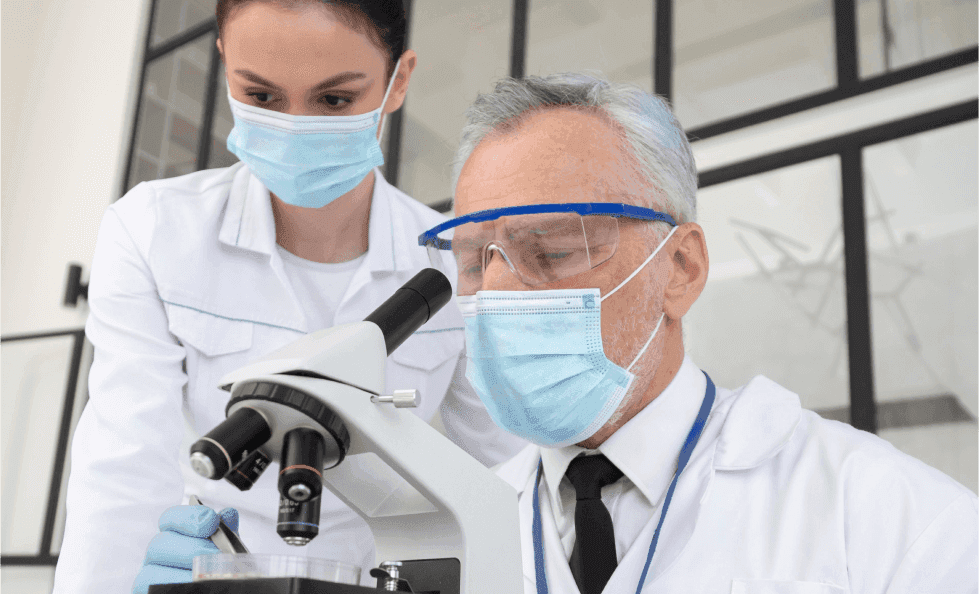
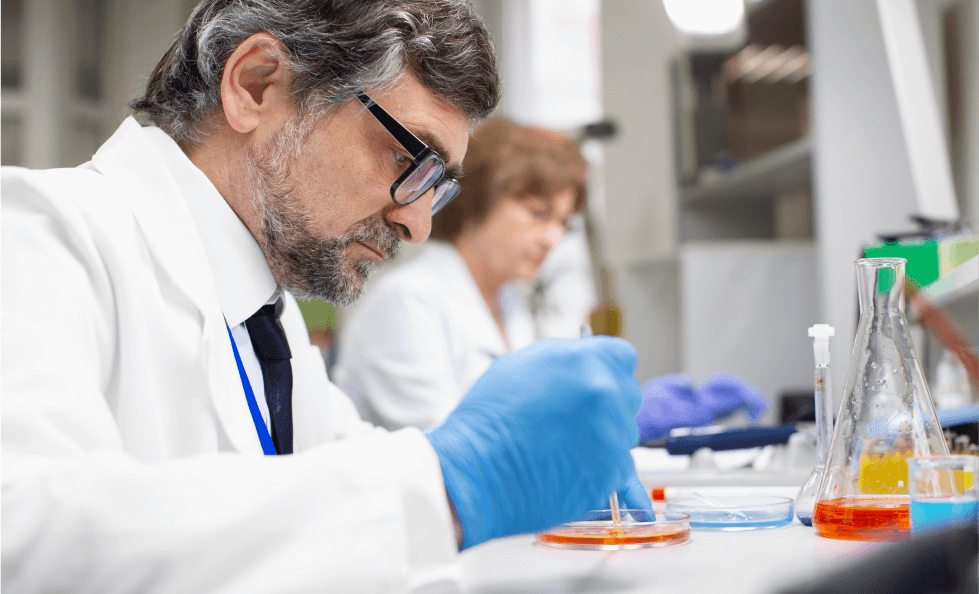
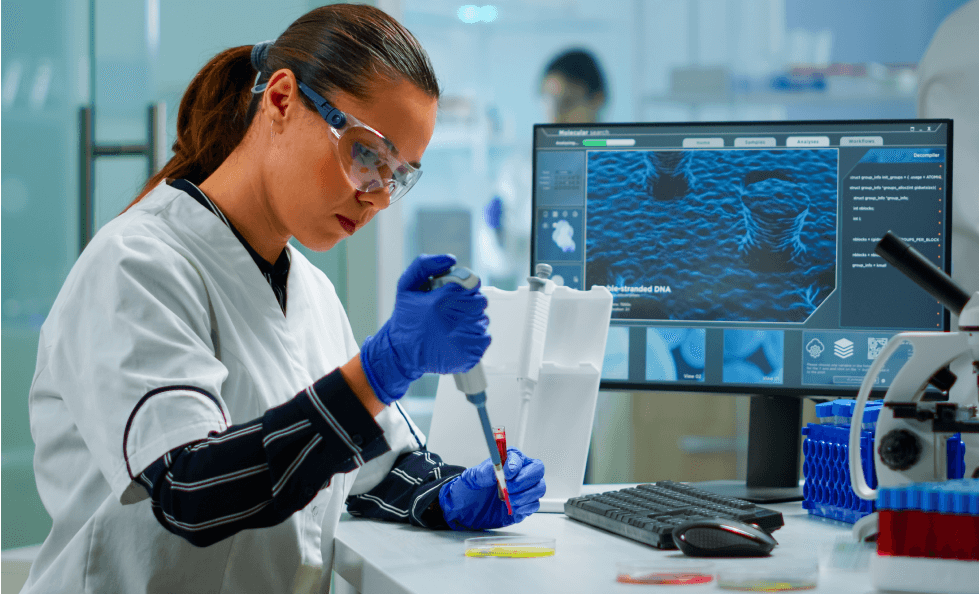
Explore More
In the cosmetics industry, safety
Evidently, with the expanding cosmetics
In the competitive world of